O polskim wkładzie w globalny program Connected Breweries opowiada nam Michał Chylewski, Specjalista ds. analityki danych produkcyjnych IIoT z Browaru w Warce, biorący udział w tym absolutnie unikalnym projekcie rozwoju i innowacji w świecie Heinekena.
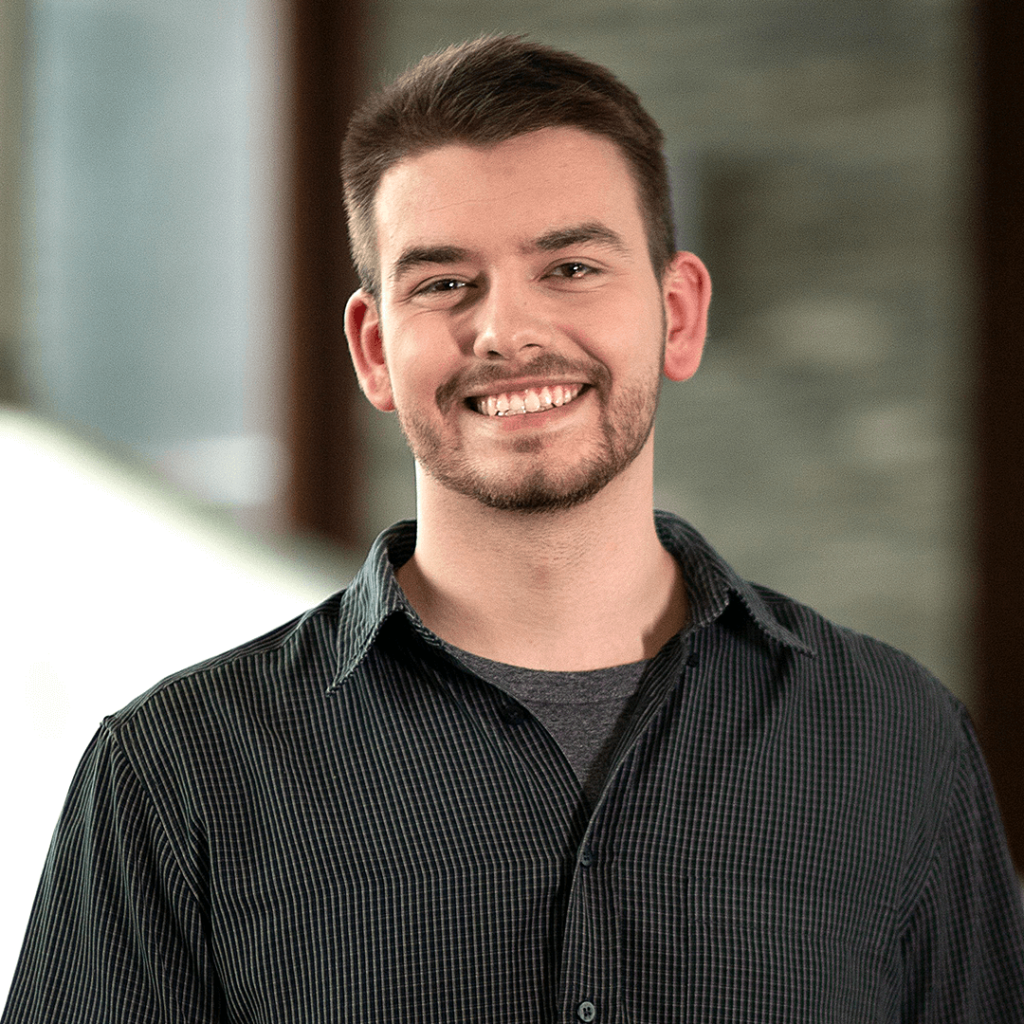
Co to jest Connected Breweries? Jak być innowacyjnym w sposób zaplanowany?
Działanie platformy Connected Breweries to kilka kluczowych obszarów: przemysłowy internet rzeczy (IIoT), czyli połączenie maszyn z internetem w zakresie dostarczania informacji i ich analizowania w czasie rzeczywistym, narzędzia skupione na pracownikach, zbiorczo określane jako Connected Worker, a także druk 3D, który obecnie jest bardzo ważnym elementem naszych działań.
Każda nowa technologia może być przez nas wykorzystana, a potem migrowana w ustrukturyzowany sposób i przeniesiona niskim nakładem pracy na analogiczne lokalizacje. Cała infrastruktura jest bardzo powtarzalna i łatwo skalowalna – use case, który został opracowany u nas może wylądować za dwa dni w każdym innym browarze Connected Brewery.
Ostatnio podłączaliśmy 31. browar do całej tej sieci – to była Vialonga w Portugalii. Przez najbliższy rok ta liczba ma się podwoić, a później kto wie, może zostanie to wdrożone w całym świecie Heinekena. To, co robimy dziś w tym zakresie jest bardzo ważne, prawdziwie rewolucyjne i nadaje ton rynkowi. Polska ma podłączone do systemu 3 browary – Warkę, Żywiec i Elbląg, więc obecnie Polska stanowi niemal 10% wszystkich browarów biorących udział w projekcie.
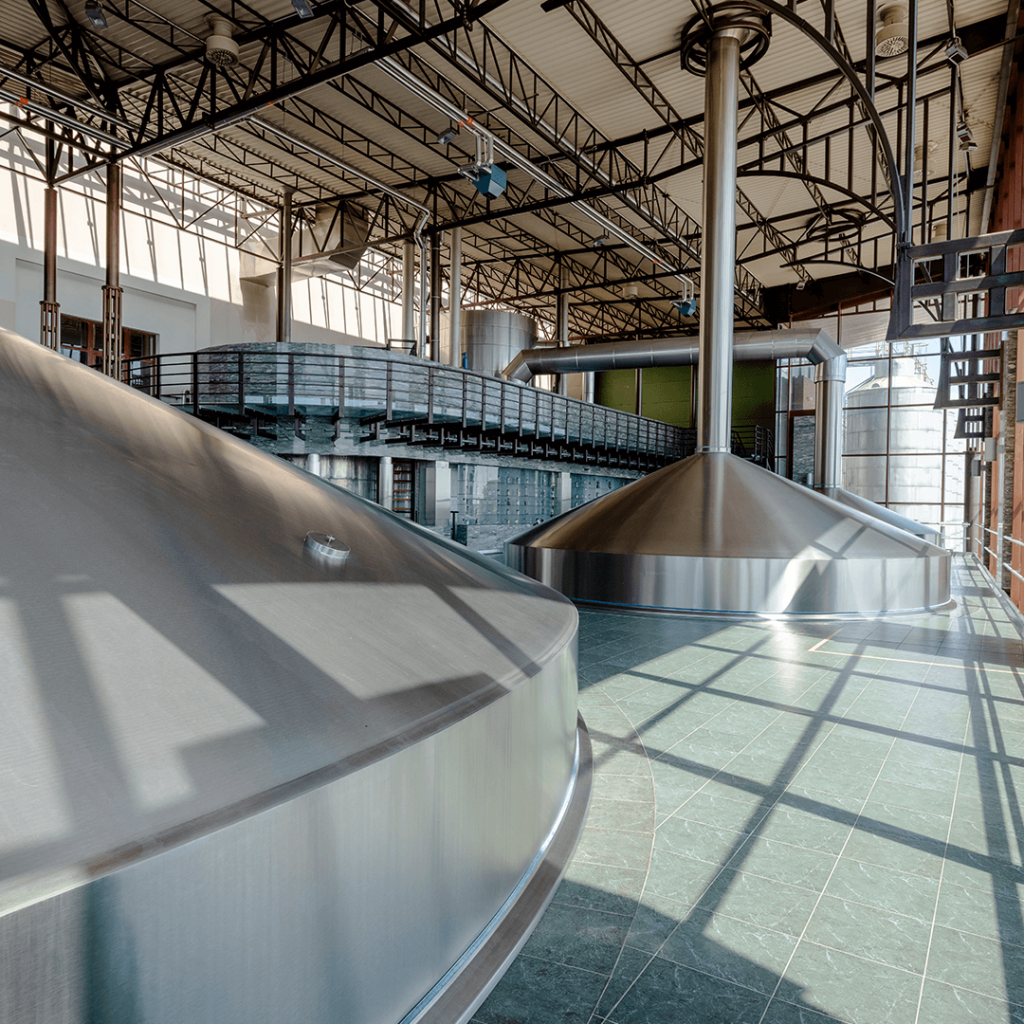
W jaki sposób browar w Warce zdobył ten wyjątkowy status w tym innowacyjnym projekcie?
Connected Brewery ruszyło w Warce w 2019 roku. Zostaliśmy jednym z trzech pilotażowych browarów tego programu, obok Ho Chi Minh (Wietnam) oraz Monterrey (Meksyk) – to tzw. lighthouse, wskazujące innym drogę w digitalizacyjnej przygodzie. Dołączając do programu browar w Warce był już zaawansowany technologicznie, miał dużą samodzielność i posiadał już srebrną odznakę TPM – nasza pozycja w owym czasie zdecydowała, że mogliśmy wyznaczać kierunki rozwoju i kreować trendy.
Heineken daje nam ogromne możliwości – jedne browary tylko przysposabiają nowe technologie, ale są takie jak Warka, które mają pełne prawo i możliwości eksperymentowania, szukania nowych dróg. Mają nadawać tempo i wdrażać nowe technologie do powszechnego użytku. Lighthouse to taki szalony doktor, który eksperymentuje sobie z technologiami. Czasem weźmiemy coś, czego nie potrzebujemy, czasem mamy czegoś za dużo, czasem rozminiemy się z celem, który był wcześniej zakładany, ale pozycja eksperymentatora pozwala nam dosyć odważnie wchodzić w nowe rozwiązania. Nie wszystko musi się przyjąć, nie każdy pomysł wypali, na niektóre rzeczy nie jesteśmy jeszcze gotowi, ale rola lighthouse to nie poddawać się, ciągle eksperymentować, wymyślać, szukać ulepszeń. Trzeba być energicznym. Trzeba lubić dużo mieć dookoła siebie, bo każdy z tych tematów trzeba trochę zgłębić, żeby się komfortowo w nich poruszać, ale jeżeli się to już zrobi, to jest zupełnie niepowtarzalna przygoda!
Opowiedz więcej o Connected Worker. Dlaczego ten element jest tak istotny?
Connected Worker to innowacja skupiona na człowieku. Taki podłączony pracownik przyszłości będzie miał dostęp do otaczającej go sieci, czy to urządzeń, czy to systemów, które go będą wspierać w codziennej pracy.
Obecnie mamy trzy aplikacje z nurtu Connected Worker. Pierwsza z nich to nowoczesny model informacji szkoleniowej – Swipe Guide. Służy do dzielenia się dokumentacją, która może być edytowana, zmieniana i dostosowywana w dowolnym momencie. Znajdziemy tam także interaktywne poradniki, które mogą być oceniane, redagowane, mogą być dopuszczane do użycia albo nie. Elementy tej aplikacji mogą być osadzane i wykorzystywane w innych miejscach, wszędzie tam, gdzie okazują się potrzebne. W ten sposób tworzymy współdzielone zasoby wiedzy, które nie są jakimiś papierowymi dokumentami, ani Excelem czy Wordem z lat 2000 – jest to technologia, która idzie w kierunku błyskawicznego dostępu do informacji, błyskawicznej edycji i dostosowywania się do ciągłych zmian.
Druga aplikacja – One2Improve – zajmuje się procesami TPM. Pozwala nam z pełnym zrozumieniem organizować ustandaryzowane zadania takie jak audyty, zgłaszanie nieprawidłowości, kontrole, zarządzanie zagadnieniami BHP. Są to rzeczy, które występują w każdym browarze i TPM doskonale sobie z tym radzi.
No i w końcu od procesów bardziej powtarzalnych mamy Parsable – tutaj znajdujemy przypomnienia o wszystkich planowych działaniach takich jak: przeglądy, prace serwisowe, czyszczenie, lubrykacja, inspekcje, itp. Dodatkowo możemy przygotować połączenie każdego zadania z przepływem krok po kroku, a nawet dodać precyzyjną instrukcję wykorzystując Swipe Guide, o którym już mówiłem.
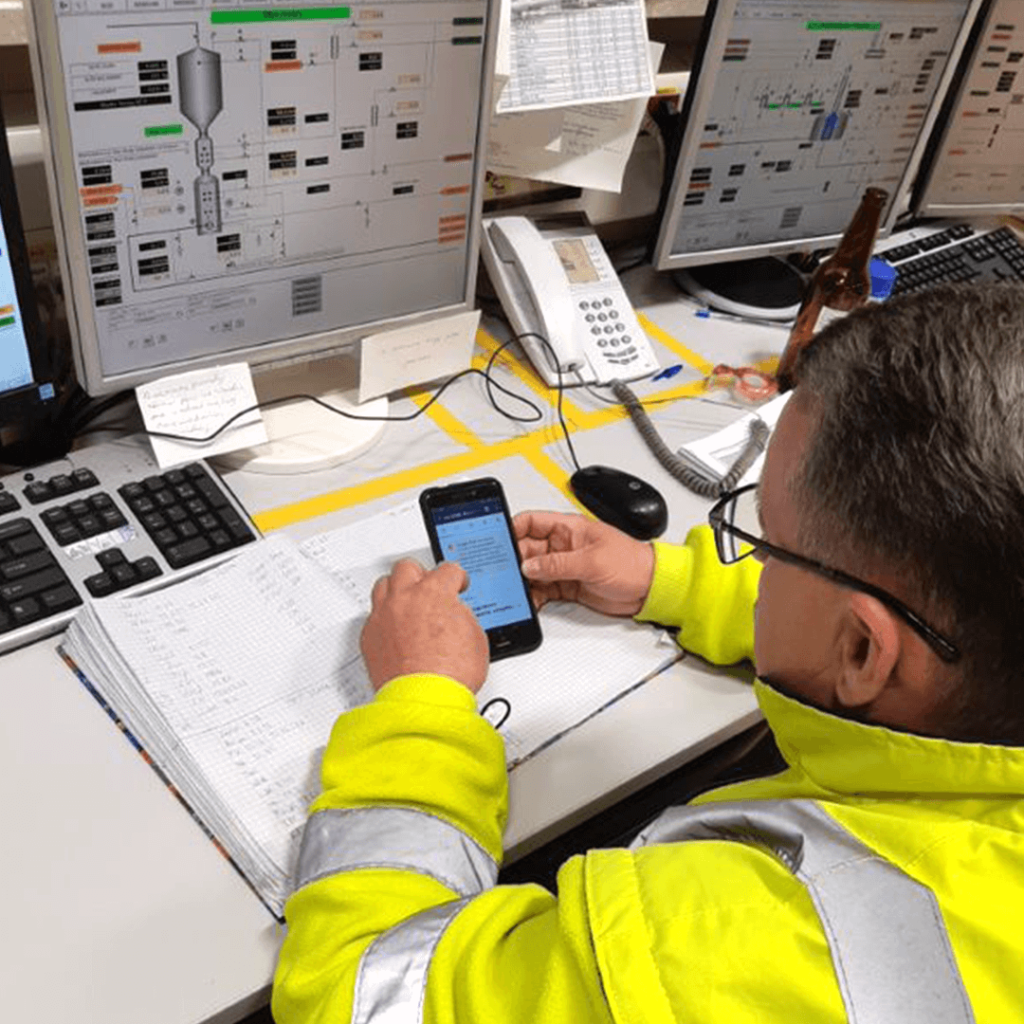
Przemysłowy Internet rzeczy, co to takiego i dlaczego jego znaczenie w nowoczesnych browarach jest tak duże?
Ktoś mądry kiedyś powiedział, że same dane nie czynią żadnej firmy mądrą, to co jest ważne i stanowi wartość dodaną dla organizacji, to płynące z tych danych obserwacje i nowe fakty. Więc my zbieramy dane z naszych sterowników przemysłowych, czyli komputerów w każdej z maszyn, które mamy na swoich liniach, stamtąd trafiają one do chmury, a na kolejnym etapie są obrabiane w taki sposób, żeby wyłuskać z nich to, co jest nam najbardziej potrzebne. Poprzez właściwą obróbkę możemy te dane potem przedstawić w użytecznej, zrozumiałej formie naszym operatorom czy inżynierom. Możemy też zamknąć we fragmencie kodu czy algorytmie odpowiedź na konkretne sytuacje, która potem może być automatycznie wykorzystywana tysiące razy bez konieczności angażowania kogokolwiek.
Kiedyś pracownicy musieli przeprowadzać takie analizy samodzielnie, w wersji papierowej i na ich podstawie podejmować akcję, teraz po prostu otrzymują alert, gdy jakieś zdarzenie ma miejsce i ich rolą jest zareagować na tę informację, nie muszą sami wykryć anomalii.
System, który rozwijamy, pomaga odciągnąć uwagę naszych pracowników od czynności, które są powtarzalne czy monotonne. Poprzez wiedzę, którą nasi ludzie posiadają, my jesteśmy w stanie takie systemy rozwijać, skutecznie formułować te wszystkie zadania. Wymaga to pewnej dojrzałości, żeby w prawidłowy sposób znaleźć źródła problemu, sformułować je, a potem znaleźć takie rozwiązanie, które może potem skopiować komputer. My w Warce to potrafimy, a wypracowane przez nas rozwiązania są potem łatwe do wdrożenia w innych lokalizacjach.
To jest technologia, którą widać w użyciu, to coś namacalnego. Pracę, którą wykonuje się zza biurka, tworząc chociażby model analityki danych, za chwilę można podziwiać w akcji na linii produkcyjnej. A jak rozwiązanie się sprawdzi, to można w krótkim czasie zobaczyć jak jest udostępniane w całym świecie Heinekena globalnie. Ta praca daje takie fajne poczucie, że to nie tylko teoria, ale można swoje dzieła zobaczyć w realnym świecie, sprawdzić jak się zachowują w praktyce i co się z nimi dzieje dalej.
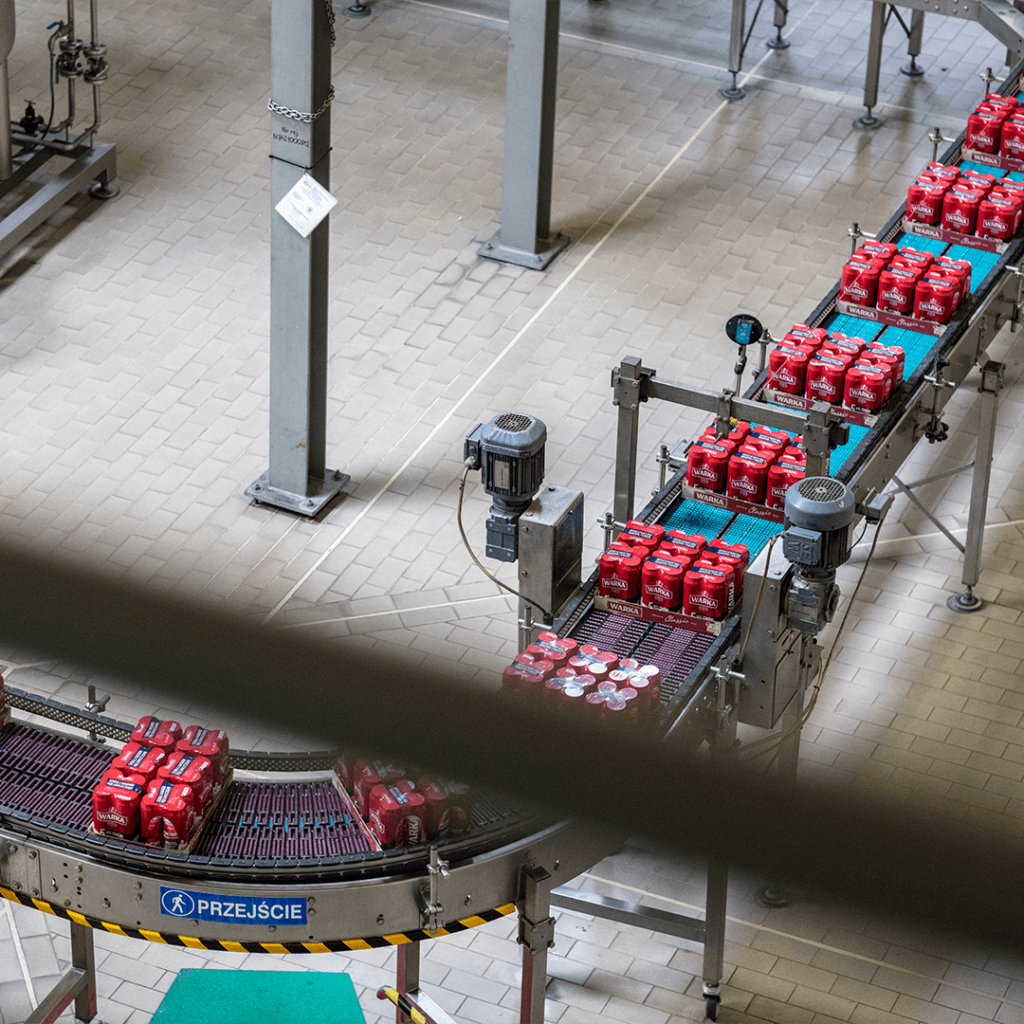
Możesz podać przykład takiego wdrożonego rozwiązania?
Ostatnio potrzebowaliśmy doraźnego rozwiązania dla problemu występującego na jednej z linii w naszym browarze – user case Minor Stop and Speeed Looses Analysis (MSSL). Była to pierwsza okazja, żeby zapoznać się z tym, jak możemy wykorzystać w praktyce świat przemysłowego internetu rzeczy – mogliśmy przedstawić, jaki mamy problem i zastanowić się, jakie dane mogą nam pomóc w jego rozwiązaniu.
Nasz model produkuje informacje o powiązaniach między zatrzymaniami maszyn, czyli buduje sobie siatkę przyczynowo skutkową i próbuje przewidzieć jak mógł wyglądać łańcuch zdarzeń na linii, który spowodował przestój. Taka analiza wymagałaby pomiarów ze stoperami, świetnej znajomości procesu, widoku z lotu ptaka na całą linię, żeby móc takie powiązania wyłapywać, a tutaj dzieje się to na podstawie odczytów prędkości czy liczników poszczególnych maszyn. Dzięki jego wykorzystaniu nasi inżynierowie mogli spojrzeć na problemy, z którymi się borykali z trochę innej perspektywy – wyrachowanej, statystycznej, matematycznej, maszynowej, ale jednocześnie takiej, której żaden człowiek nie był świadomy. W 2020 roku za ten projekt została nam przyznana nagroda Heineken Supply Chain Award w kategorii Digital za bardzo skuteczną walkę z mikroprzestojami na liniach produkcyjnych.
Mamy też model Anomaly Detection, czyli taki statystyczny wzorzec, który w czasie rzeczywistym dogląda stanu pracy elementów elektrycznych czy mechanicznych takich jak serwa, czy silniki. Analizuje, jak ta praca powinna wyglądać, porównuje stan obecny z wzorcem i na tej podstawie wnioskuje, czy odchylamy się od pewnej założonej normy czy jeszcze jesteśmy w granicach rozsądku blisko tego celu. Jeśli od niego odbiegamy, nasz model jest w stanie samodzielnie i automatycznie zaalarmować operatora. Jest w stanie nas poinformować o tym, że coś jest nie tak, że coś się zbliża, dużo szybciej niż dostrzegłby to człowiek.
Ważny element, o którym warto wspomnieć, to fakt, że dzięki chmurze odblokowujemy połączenia pomiędzy naszymi istniejącymi systemami – poszczególne maszyny produkcyjne to często samotne wyspy, ale łącząc dane z nich w jeden system otrzymujemy pełniejszy obraz.
Dziękujemy za rozmowę!